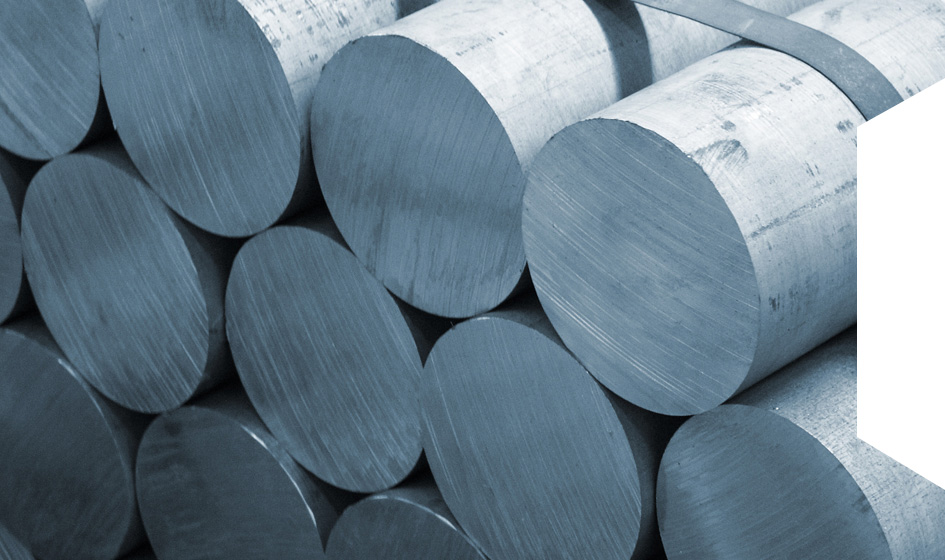
Substrates
Aluminium
Physically, chemically, and mechanically, aluminium has very similar qualities to steel, copper, and lead. It can be easily shaped, formed, and fabricated. Perforated aluminium sheet is one third the weight of steel but has a comparable strength to weight ratio. It is lightweight, ductile, able to withstand low-temperature conditions, and corrosion resistance makes it ideal for perforated metal processing.
Mild Steel
Mild steel is not an alloy steel and therefore does not contain large amounts of elements besides iron. As the carbon and alloying element content are relatively low, it is typically more ductile (easy to punch), machinable, and weldable than high carbon or alloy steels. However, it also means it is nearly impossible to harden and strengthen through heating and quenching. The lack of alloying elements such as those found in stainless steels means that the iron in mild steel is subject to oxidation (rust) if not properly coated. The popularity of this material is due to the negligible amount of alloying elements which allow the material to be more economical when compared with other steels.
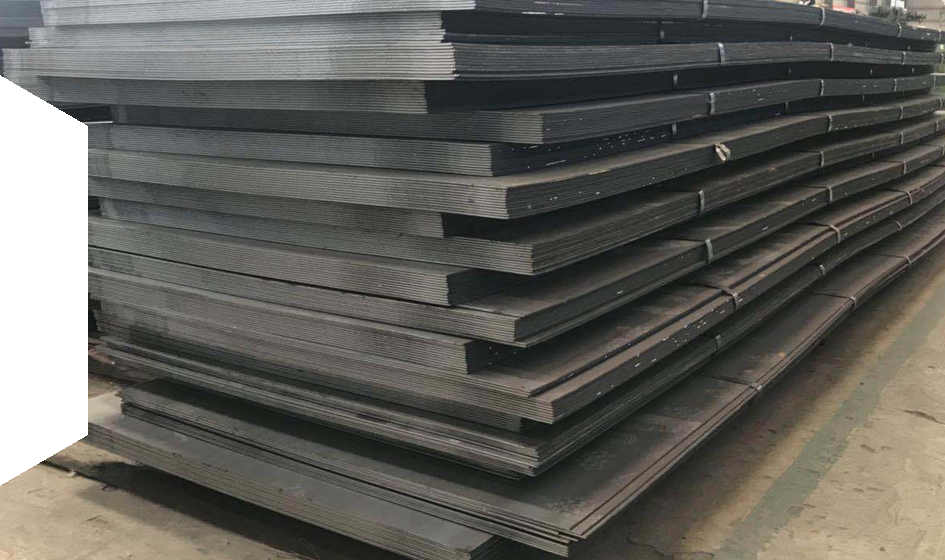
Mild Steel Sheet
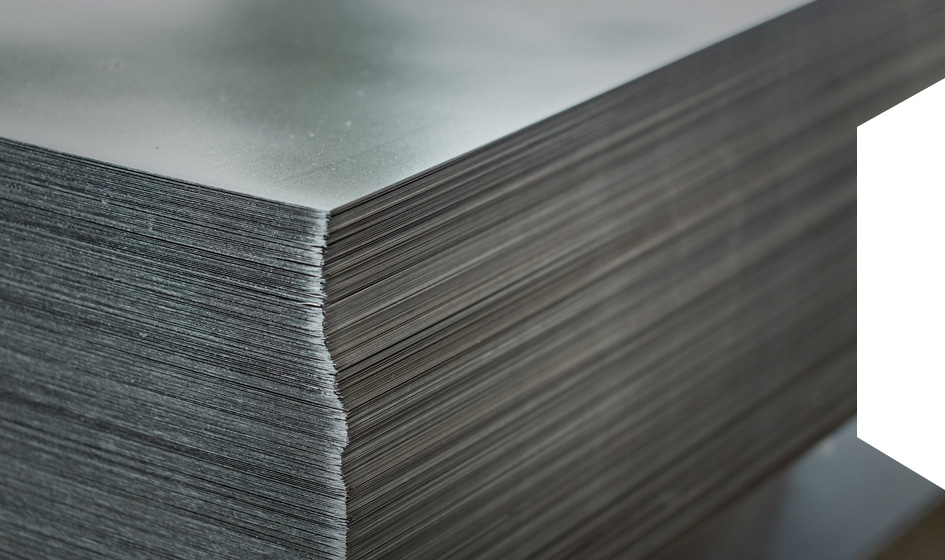
Hot Dipped Galvanised Sheet Metal
Galvanised Steel
The manufacture of galvanized steel involves hot dipping steel in a galvanizing solution that coats the metal and protects it against abrasion, corrosion, and offers long term surface protection. The process adds long life, durability, and excellent performance. However, the moment a perforation is punched in the material, the whole piece will lose it’s protective quality as un-galvanised sections are exposed. 3D Embossing will preserve the galvanised process of the material.
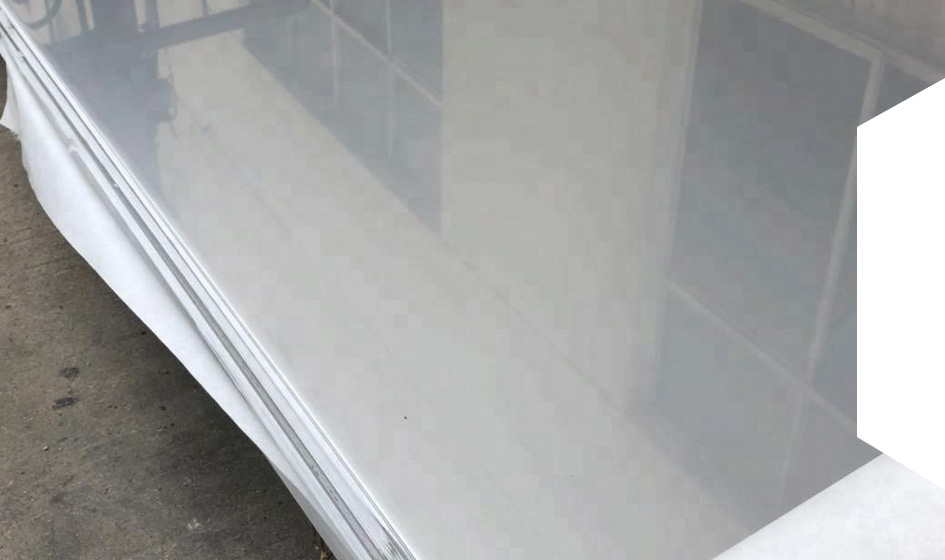
Stainless Steel
The 3 main types of stainless steel are austenitic, ferritic, and martensitic. As a premium product, stainless steel is corrosion, rust and bacteria resistant as well as being lightweight and strong. Its applications extend into hospitality and food production.
HW350/ Corten
An oxidised finish on a Steel substrate that eliminates the need for painting. The material gets its name from its two distinguishing properties – CORrosion resistance and TENsile strength. The finished treatment gives a weathering, rusted appearance.
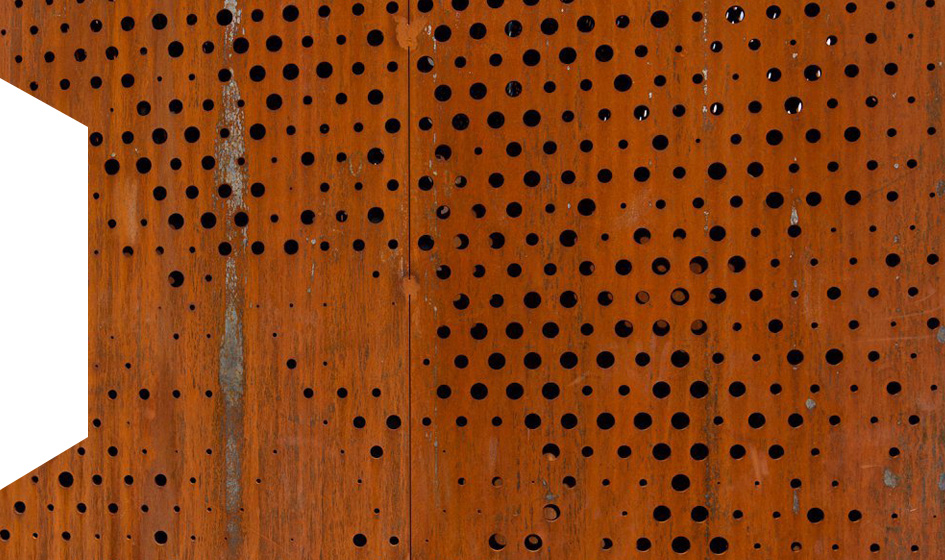
Product | Application | Surface finish | Material density | ||
---|---|---|---|---|---|
Substrate | Interior | Exterior | Powder coat | Anodising | |
Mild Steel | ![]() | ![]() | 7.85 | ||
Galvanised Steel | ![]() | ![]() | 7.85 | ||
Aluminium | ![]() | ![]() | ![]() | ![]() | 2.71 |
Stainless Steel | ![]() | ![]() | 8.18 | ||
HW350/Corten | ![]() | 8.20 |
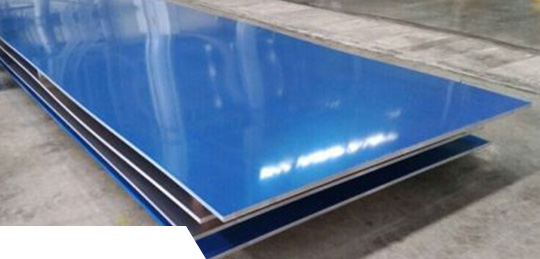
PE Coating
Some materials (Aluminium, Stainless Steel & pre-coated Steel ) can be ordered from the mill with different plastic films applied for surface protection. There are significant differences in purpose and performance of the plastic films. The films are intended to protect the surface of the material from scratches and scuffing during handling and working prior to and during installation. They should be removed during service. Please discuss any particular surface treatment request with one of our technical sales staff.
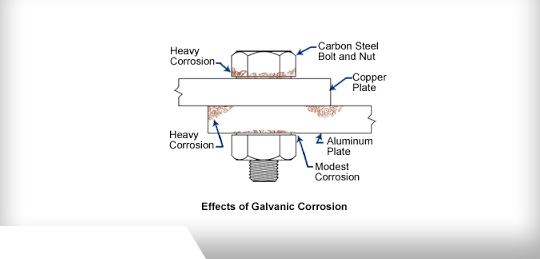
Dissimilar Metals - The Importance of Consideration
When using dissimilar metals in a fabrication project, precautions must be taken to prevent galvanic reaction. This occurs when two different metals are in contact in a corrosive or conductive environment and the current flow changes. When two dissimilar metals are involved, the reaction is called galvanic corrosion.
Why Exactly Does Galvanic Reaction Occur?
When one metal contacts another, a current flow transfers between the 2 metals. The current flow changes when dissimilar metals come in contact with each other. The corrosion rate of the active, or least corrosion-resistant metal, accelerates and the inactive, or more corrosion-resistant metal, decreases.
The further apart the metals are on the corrosive scale, the stronger the galvanic reaction between the two. Similar metals have little effect on each other.
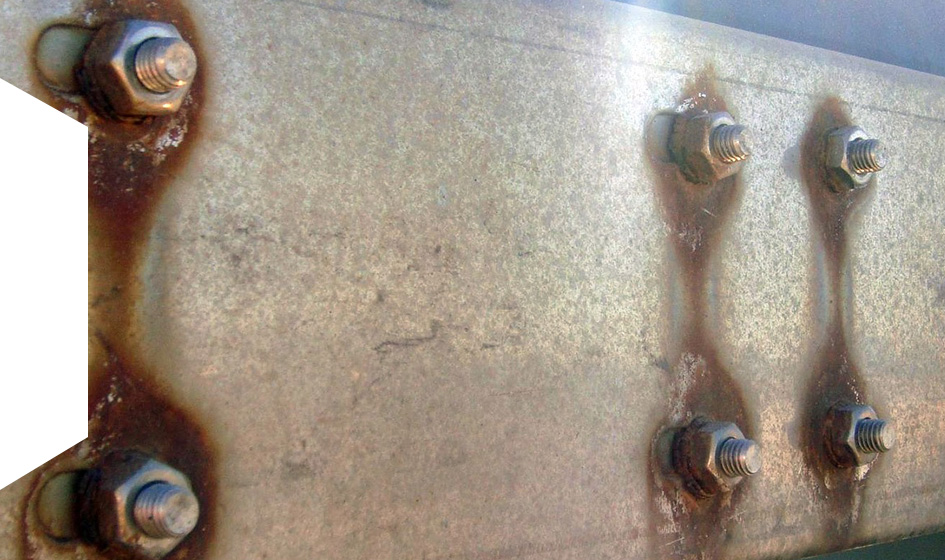
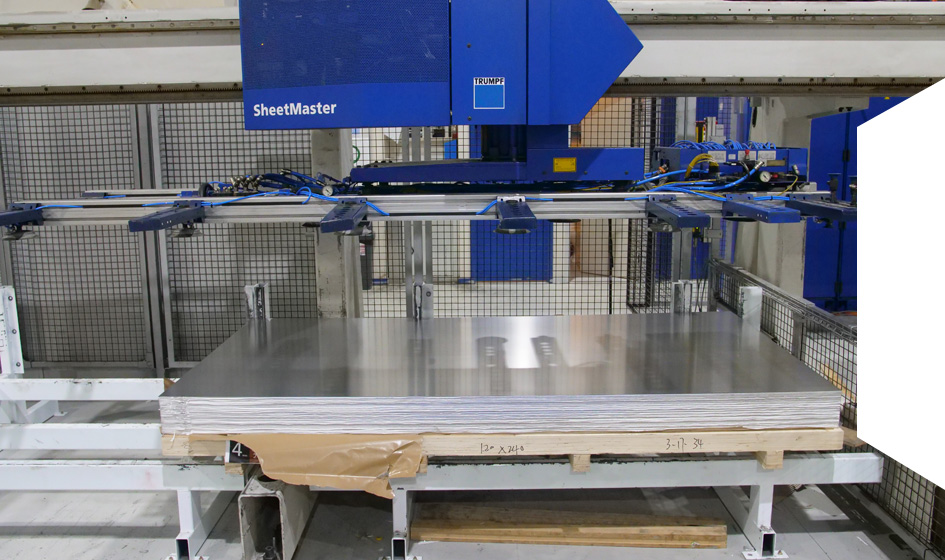
Moisture is a key element affecting galvanic reaction. The relative surface of dissimilar metals used in a metal fabrication project should also be taken into consideration. For example, using inactive metals as the main body of the project, joined by active connectors, could cause the joints or fasteners to corrode at a quicker rate.
In this case, it may be recommended to connect two sections of similar metals with fasteners also made of the same metal. If using similar metals isn’t possible, a compatible metal is the next best choice. Metrix Group are well versed in dissimilar metal prevention and are happy to help consult on the best combinations for your project.